Our engineering teams have the latest equipment and technical ability to scan, reengineer, predict life, and propose liner improvements to support customers’ desired outcomes, whether extended life, improved throughout, or product shape. Working with customer data, partner foundries, and our quality team to ensure the final product meets or exceeds expectations.
Our engineering is continuously working on innovative designs and materials to improve products to maximize our wear parts’ value. We follow the Six Sigma methodology in design engineering to provide a consistent and practical approach to maximise the life and usability of our wear parts. We continue to improve our processes to help customers realise cost-effective solutions that extend life through clever design and thorough quality inspections.
ENGINEERING SOFTWARE
The benefit of accurate 3D scanning in conjunction with our predictive software is that the customer receives an improved liner profile suited to the application that will fit as expected. The ease of installation means equipment is up and running faster, providing customers with a convenient and reliable solution.
Our team uses the latest recommended 3D analysis software and quality control software to identify potential design concerns before casting the part. The software allows our teams to make designs as accurately as required to realize the perfect fit and profile. When it is time to cast the customers’ liner or part, MWP is confident knowing that the drawings provided will result in an accurate fit, correct profile for the application, and of high-quality thanks to the mature relationships we have with our foundries.
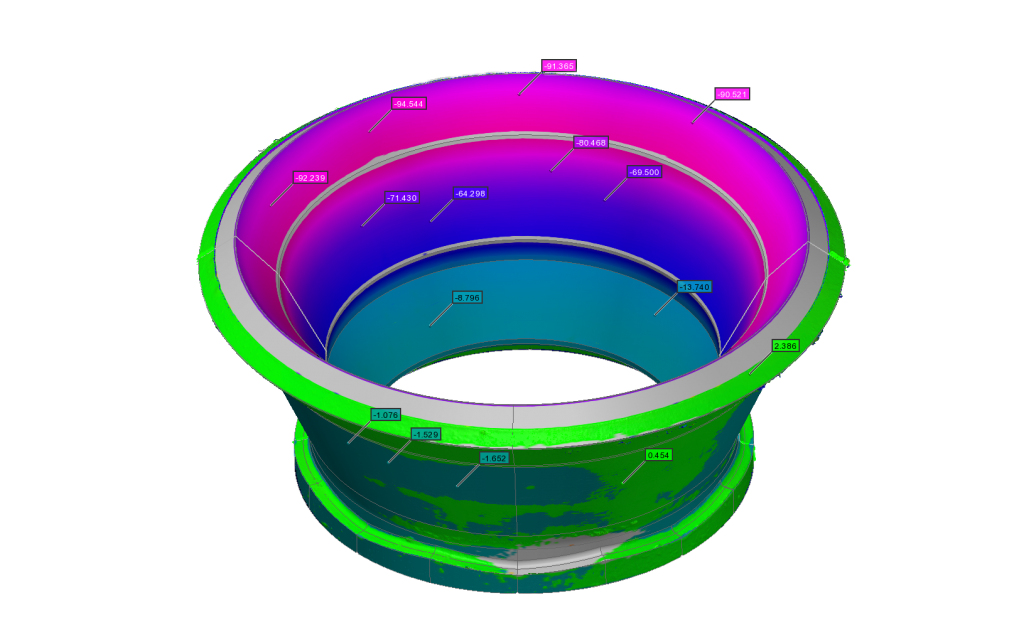
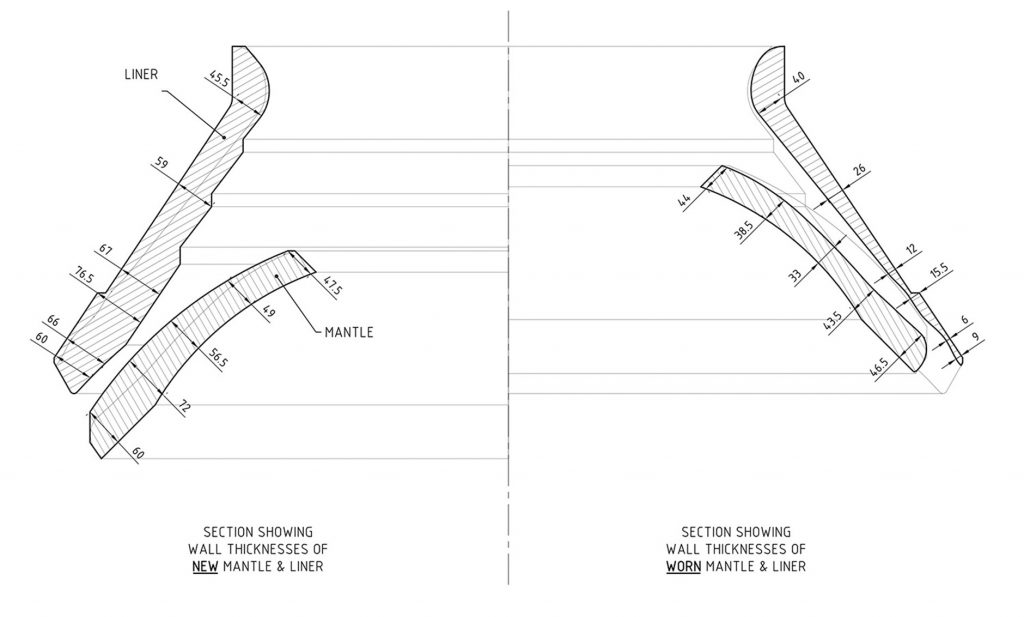
QUALITY CONTROL
We believe in built-in quality rather than only product quality, and we employ the Six Sigma methodology to achieve it. Quality control is embedded in our process resulting in a reliable and accurate final product. Our suppliers also follow the same philosophy that our quality engineers continuously monitor. We believe in capturing ‘The Customers Voice’ for continual quality improvement.